The Stockinette stitch, also known as the Stocking stitch, is a fundamental Knit-Purl pattern that forms the bedrock of countless knit designs. It’s the stitch pattern that conjures up soft images of warm, snugly knit sweaters in our minds. Essentially, the Stockinette stitch isn’t a singular stitch, but a pattern sequence consisting of individual knit and purl stitches.
The Versatility of Stockinette Stitch
The Stockinette stitch is widely adopted by knitters globally due to its versatility and popularity. It forms the basis of numerous knit items such as t-shirts and commercially produced socks. Despite its ubiquity, mastering the Stockinette stitch is vital as it enhances your understanding of the knitting process and equips you to decipher stitches on a needle proficiently. Transitioning from the intricacies of the Stockinette stitch, let’s delve further into the distinctions between knit and woven fabrics.
Technical Aspects of Stockinette Stitch
The Stockinette stitch, commonly abbreviated as St St in knitting patterns, is a fundamental technique that forms the backbone of many knitting projects. This stitch is achieved by creating a precise sequence of alternating knit and purl stitches. The resulting texture is distinctly smooth and has a classic appearance, often recognized even by those new to the craft.
The process involves knitting the knit stitches and purling the purl stitches, which sounds straightforward but demands attention to detail and a steady hand. For beginners, mastering the Stockinette stitch is both a rite of passage and a test of their developing skills, requiring them to carefully monitor their work to maintain the uniformity of the fabric. This stitch not only lays the foundation for more complex knitting patterns but also teaches valuable lessons about tension and consistency in knitting. The Stockinette stitch is versatile, serving as the basis for numerous garment designs and styles, and is a key component in understanding the structure and behavior of knitted fabrics.
Knitted Fabrics: Structure, Uses, and Identification
Knitted fabrics are a fascinating and diverse group within the textile world, characterized by their unique construction of interlinked yarn loops. This looping technique imparts a natural elasticity to the fabric, making it stretchy and flexible regardless of the inherent elasticity of the yarn used. These fabrics can be meticulously crafted by hand, a skill often highlighted in tutorials like Marissa’s guide on the Knit Stitch. Alternatively, they can be produced on a larger scale through machine knitting. Both methods involve the use of needles, but the tools differ significantly in their design and function between hand and machine knitting.
The essential building block of any knitted fabric is the “stitch”, which comes together to form a distinctive grid-like pattern. This pattern is composed of horizontal lines of stitches, known as rows in the handknitting community, or courses when referring to machine knitting. The vertical lines in this grid are called wales. This structural arrangement of stitches gives knitted fabrics their unique properties and appearance. While some knitted fabrics are designed to be reversible, offering the same look and feel on both sides, most have clearly defined right and wrong sides. This characteristic is integral to the design and functionality of the fabric, affecting how it drapes, stretches, and ultimately, how it is used in garments and other textile products. The rich variety of knitting techniques allows for a wide range of textures, patterns, and strengths, making knitted fabrics a versatile choice for many applications, from clothing to home textiles.
Knit fabrics are favored in items that benefit from their inherent stretchiness, such as sweaters, socks, T-shirts, swimwear, activewear, stuffed toys, office chairs, and even car ceiling fabrics.
To identify a knit fabric, look for these features:
- Easy stretching in one or more directions;
- A surface pattern of flat “Vs” or bumps;
- Continuous yarn loops.
There are various types of knit fabrics. For instance, a men’s white sleeveless undershirt often uses ribbed fabric (with knit and purl stitches on the same side) unlike a standard T-shirt. Similarly, hoodie sweatshirts and T-shirts are knitted but differ in the thread or yarn weight used.
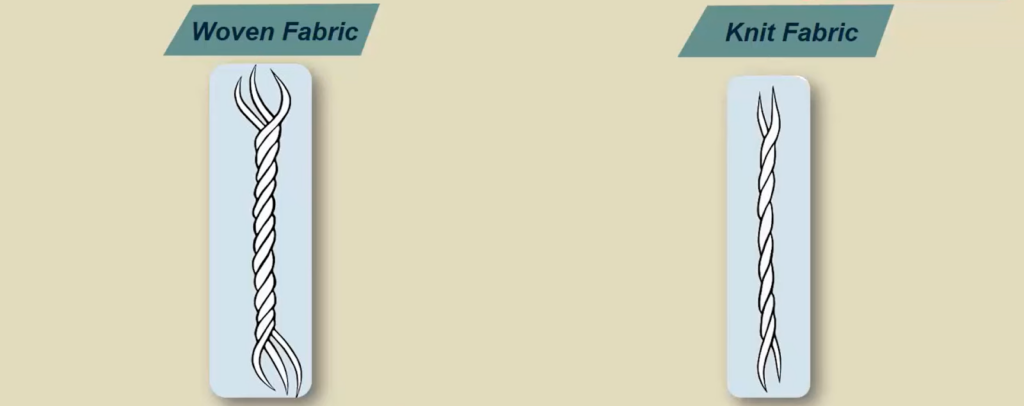
Woven Fabrics
Woven fabrics come into existence through the intertwining of two sets of yarns positioned at right angles to each other. The natural stability of woven fabrics is a result of these intricate interlacings, rendering them non-elastic unless elastomeric yarns are incorporated. The creation of woven fabrics extends from manual handweaving using table or floor looms to the utilization of larger industrial looms.
In woven fabrics, the grainline adheres to the warp direction, constituting the vertical orientation of the fabric. For the proper draping and fit of clothing, it is essential to cut sewing patterns “on the grain,” preventing undesirable stretching along the diagonal (the bias) and ensuring a comfortable and well-fitted outcome.
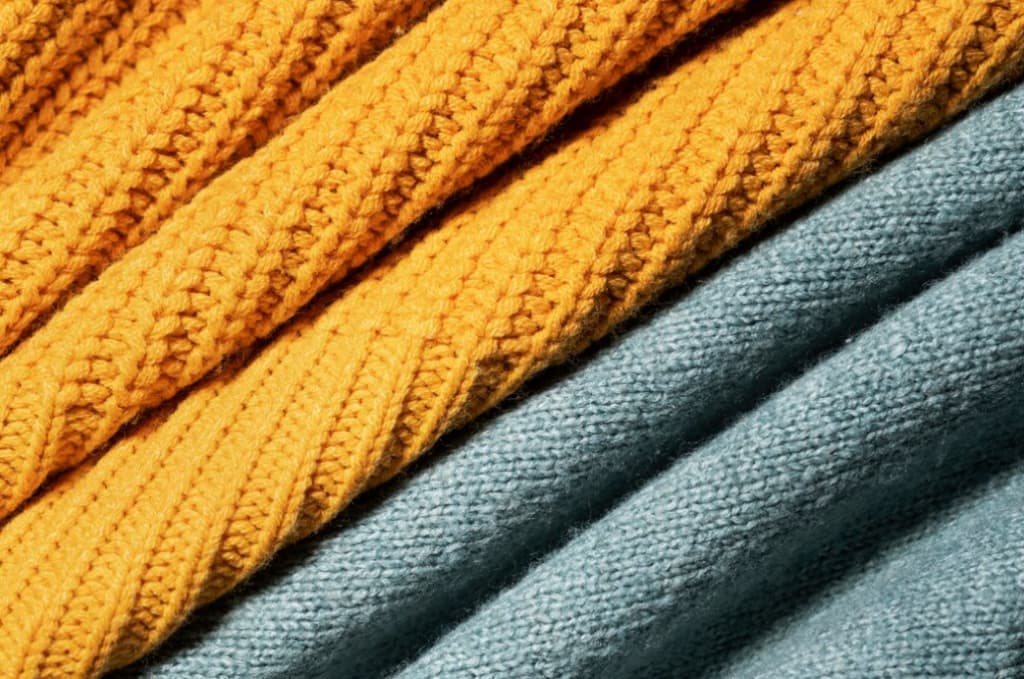
Selvages form the left and right boundaries of a fabric, running vertically along its edges. You might also see them spelled as ‘selvedges’—both are correct. Selvages range from being a mere final stitch or interlace at the fabric’s edge to a tightly-woven strip that lends stability to the primary, usable portion of the fabric. Retaining both selvages on a fabric piece is advisable for optimal use.
Selvages are invaluable for “fabric detective” work, aiding in determining the fabric’s grain or the correct orientation of a print. The distance between selvages typically defines the maximum width of a fabric piece. While lengthening is feasible, the width is constrained by the size of the machine used for knitting or weaving the fabric.
Woven fabrics, recognized for their stability, are commonly used in products like jeans, button-down shirts, quilts, couches, curtains, rugs, and tarps.
To identify a woven fabric, look for these characteristics:
- Tendency to unravel along cut edges;
- Limited stretchability;
- Clearly visible intersecting yarn sets at right angles.
Nonwovens
Nonwoven fabrics diverge from traditional textiles as they consist of individual fibers intricately entangled, felted, or bonded together, eschewing the conventional use of yarns. Their inherent characteristics often include lower stability and a propensity to separate more readily compared to woven and knit fabrics.
The versatility of nonwovens finds expression in various applications, ranging from the realm of felt crafts to the production of wet wipes, weed barrier fabrics, and other landscaping textiles.
Embarking on a quest to identify nonwovens? Keep your detective hat on, as these key characteristics may signal the presence of a nonwoven fabric:
- Lack of a distinguishable right or wrong side;
- Absence of a discernible direction;
- Ease of separation or pulling apart.
Conclusion
Comparing Knit vs Woven fabrics unveils their distinct features and uses. The Stockinette stitch is a cornerstone in knitting, contributing to versatile knit items. Knitted fabrics provide inherent stretchiness for various products, while woven fabrics, prized for stability, are common in items like jeans. Lastly, nonwoven fabrics, crafted from entangled fibers, exhibit lower stability but serve diverse purposes. Recognizing the unique traits of each fabric type enables confident identification, distinguishing between knits, wovens, and nonwovens with precision.